Dow Chemical is Making their Supply Chain More Resilient With a Centralised Communication Platform
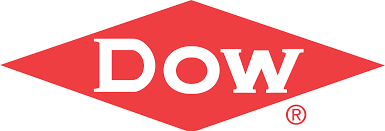
A few years ago, supply chain risks mostly meant component shortages, price volatility and supplier failures. Countering these threats was relatively easy for companies. The trick was to simply identify the loopholes and plug them up with strategic measures like dual sourcing and supplier collaboration.
This stopgap solution is no longer effective. Today, businesses stand amidst widespread political cataclysm and populism imposed by nations that are determined to implement stringent protectionist policies against free -trade. The reality is that the new interconnected global economy has made supply chains increasingly vulnerable. Disruptions such as a minor shipment delay can be enough to cause significant financial repercussions on shareholder value. This newly emerged supply chain risk poses the threat of a total systemic collapse in the near future.
A recent Forbes report reveals that nearly one out of five supply chain professionals are concerned about terrorism, war and other geopolitical threats affecting their supply chain functions. They equate this level of anxiousness to that which arises from supplier financial issues, counterfeited products and infringement of intellectual property right.
In order to stay on guard against potential disruptions that these unstable situations might usher in, businesses need to rethink their global operation footprints and implement robust risk management measures. With newer sanctions and stringent regulatory policies coming into place, this is the next logical step towards protecting global Procurement channels.
Staying Prepared – Infusing Resiliency into Supply Chains
Organisations tend to lose resiliency in supply chain operations as they grow. With expanding business scope comes increasing complexity in the form of scattered supplier networks that are often difficult to manage. Businesses can cultivate resilience by identifying the vulnerabilities within its supply chain function and developing specific capabilities to counter the disruptions.
The Dow Chemical Company for instance, has made significant advancements in supply chain risk identification and management by strictly adhering to an Enterprise Risk Management (ERM) approach. The chemical corporation has teamed up with renowned ERM solution providers to closely understand the potential impacts of weather-related events, effects of foreign currency exchange rate movements and volatility of energy costs and purchased feedstock on supply chain operations.
During the early 2000s, the company started off with a venture to revamp its supply chain management initiatives and forge a robust B2B communication network. It was during this time that Dow approached Elemica in an attempt to devise a digital supply network. Elemica is a supply chain operation framework that leverages a high-end application database to help connect companies to their respective supply chain networks comprising of vendors, suppliers and logistics providers.
Since the start of the partnership, Dow Chemical has been highly successful with its implementation of the Elemica supply chain risk management solutions. The company has leveraged the Elemica platform to develop strong B2B networks that facilitate increased communication among stakeholders. The platform not only eradicates the risk of supplier failures but also ensures that the company gets to closely oversee the supply function even if it’s dispersed geographically.
Taking a More Targeted Approach
The Elemica solution is just one among the several steps that Dow Chemical has taken toward building a resilient supply chain function. Recently the company implemented a high-end supply chain resilience assessment and management tool known as SCRAM, which was developed by researchers at the Ohio State in partnership with U.S Air force, L. Brands and several other companies. The tool comes with a computer-based toolkit that offers a diagnostic evaluation of a company’s preparedness to deal with external change factors. The tool determines resilience gaps in supply chain and then suggests process improvements, thereby helping a company to survive the shock of an unexpected turn of events.
With organisations being dispersed globally, it has become critical for Procurement to develop smart communication networks that can condense useful business information coming from a variety of functional departments across multiple locations. SCRAM provided Dow Chemical with access to a single source of information as respondents from different areas (both geographical and functional) started answering questions pertaining to their supply chain capabilities and vulnerabilities in unpredictable situations.
The system would automatically aggregate all the answers and unveil any potential incongruity in the company’s ability to counter the disruptions. Implementing such strong and centralised communication systems with advanced applications like SCRAM has enabled Dow to cope with a continuous stream of supply chain risks, from economic turbulences and industrial accidents to natural disasters.
Building resilience in supply chain functions is not a substitute for other ERM methods. Rather, it is an ongoing process that enables companies to embrace change in a turbulent and complex environment by enriching their range of capabilities. The field of supply chain resilience is still young, so in terms of understanding the resilience of complex industrial systems and developing innovative platforms and methods to enhance enterprise resilience, there’s still plenty of room for improvement.