Measuring Procurement’s Impact on the Business
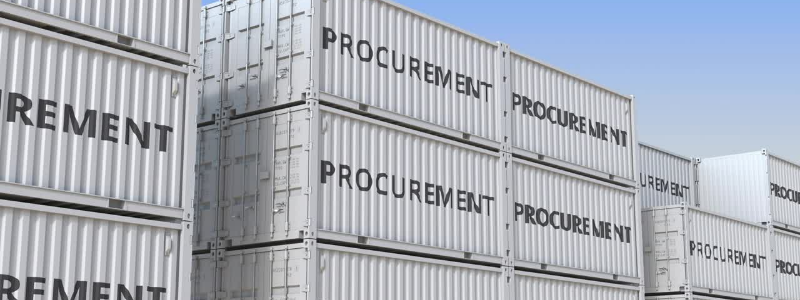
As you can see from this month’s featured news stories, procurement has the potential to have a wide and far-reaching impact on the organisation as a whole, whether that be through making environmentally-conscious purchasing decisions or freeing up budget through frugal spending.
However, in order to understand the wider impact of procurement, an organisation first needs to be able to measure its success. Historically this measurement would have simply revolved around cost savings, but this can only tell half the story when it comes to demonstrating procurement’s value to its parent organisation.
Procurement Cycle Time
This KPI is calculated by measuring the time between procurement placing a requestion and the completed order arriving at goods receiving. The best companies are able to place orders quickly and wait shorter lengths of time before it arrives. This is achieved by having efficient and streamlined processes within the organisation itself and strong relationships with proven and dependable suppliers.
Vendor Performance
Feeding into procurement cycle time, organisations need a way to ensure their suppliers are performing at the level they need to reduce that metric, while simultaneously meeting other expectations such as quality of product/service.
Factors such as delivery lead times, communication time lags, product/service quality, cost competitiveness, contract compliance, back orders and substitutions, and pricing consistency, can all be easily measured to gain a holistic picture of vendor performance.
Spend Under Management
Unmanaged spending can have a significant impact on business performance, meaning those organisations which are able to effectively track the percentage of total spend managed by procurement can, according to research, lead to benefits of between 6-10%.
Reducing unmanaged spending is a topic all of its own but focussing on these areas can help procurement reduce costs and deliver new levels of value to their organisations.
Contract Compliance
One metric which often gets overlooked, but can seriously help reduce costs, is to measure the proportion of purchase orders which are catalogue based.
When an organisation makes the majority of purchases through pre-approved suppliers with firmly negotiated terms prices tend to be lower, lead times are lower, and errors far less frequent.
In addition, by decentralising the purchase process, individuals throughout the organisation are able to place orders, which free procurement officers to seek out new suppliers and negotiate better deals.
Final Thoughts
“Measure twice – cut once” as the old builder’s adage goes.
If you want to see better performance and greater value coming out of your procurement department, consider implementing these KPIs to gain a better picture of the landscape. Research is nothing without actioning the findings however, so make sure you also have the people and process in place to leverage the largest benefit from your findings.