Can Toyota Afford to be “Lean” in the Post-COVID World?
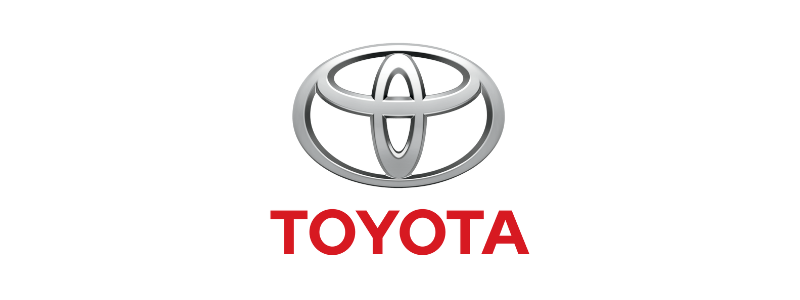
It feels like forever ago when we were championing Toyota as an innovator of lean manufacturing. The Japanese car manufacturer had pioneered a new way of keeping business waste to a minimum with its seven lean principles - overproduction, unnecessary transportation, inventory, motion, defects, over-processing, and waiting.
However, the COVID-19 crisis has exposed many of the weaknesses inherent in our reliance on just-in-time supply chains and this feeds directly into the lean manufacturing principle of keeping inventory to an absolute minimum.
Early in August 2021, a worker in a key Toyota supplier parts factory tested positive for the more virulent Delta variant of the SARS-COV-2 virus. This diagnosis caused a snowball effect which eventually led to a complete shutdown of operations at the factory. Because the factory produces a wire harness which is necessary to hold together the inner workings of a car, Toyota has been forced to slash production of new motor vehicles by 40% – all because of a single positive test.
This is leading Toyota to begin discussions on whether its lean philosophy is still appropriate in a post-COVID world and whether we can still afford to rely on just-in-time supply chains when a single case can grind everything to a halt.